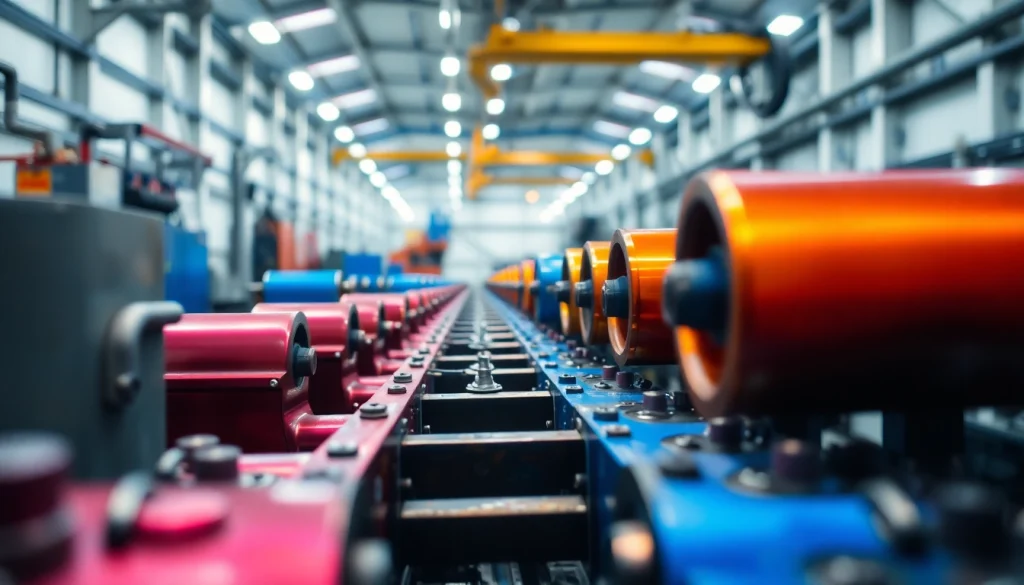
Understanding E-Coating
What is E-Coating?
E-coating, or electrophoretic coating, is a method of applying a protective layer of paint to conductive substrates through an electrochemical process. In this innovative technique, objects are submerged in a bath containing charged paint particles. An electrical current is then passed through the bath, causing the paint particles to deposit evenly onto the object’s surface. This process leads to a uniform coating with excellent adhesion, even in hard-to-reach areas. It’s commonly used in various industries, from automotive to appliance manufacturing, to enhance durability and corrosion resistance.
Benefits of Ecoating West Midlands
The West Midlands region is renowned for its advanced manufacturing and industrial capabilities. The benefits of ecoating west midlands services include:
- High-Quality Finish: E-coating provides a smooth and consistent finish that is both aesthetically pleasing and functional.
- Corrosion Resistance: This process offers superior protection against rust and environmental damage, extending the life of substrates.
- Environmentally Friendly: E-coating generates minimal waste and uses less energy compared to traditional painting methods.
- Cost-Effective: While initial investment might be higher, the long-term savings from reduced maintenance and replacement costs make it a financially sound decision.
How E-Coating Works
The e-coating process integrates several key stages that contribute to its effectiveness, including:
- Pre-treatment: Removing oils, dirt, and oxidation from the surface is crucial for achieving adhesion.
- Electrophoretic Deposition: As the paint particles migrate towards the grounded part via an electric field, they adhere to the surface.
- Curing: Once the desired thickness is achieved, the coated components are cured in an oven, which establishes the final properties of the coating.
The E-Coating Process Explained
Step-by-Step Guide to E-Coating
The e-coating procedure comprises multiple orderly steps:
- Surface Preparation: Begin with cleaning the substrates. This step can involve various methods, including alkaline cleaning or sandblasting, to ensure surfaces are free from contaminants.
- Pre-treatment: Utilize phosphating or chromating to promote coating adhesion and enhance corrosion resistance.
- E-Coating: Immerse parts in the e-coating bath. Control the voltage and current to optimize particle deposition.
- Rinsing: Remove any excess material from the component post-deposition to ensure a clean and smooth finish.
- Curing: Cure at the specified temperature to solidify the coating for ultimate durability.
Key Technologies Used
While e-coating follows the basics of electrophoretic deposition, several technologies enhance the process:
- Auto-batch Processing: Automating the process minimizes human error and maximizes efficiency.
- Advanced Curing Techniques: UV curing and infrared heating are common methods to improve the speed and energy efficiency of curing.
- Environmental Control Systems: Monitoring and maintaining optimal conditions within the e-coating bath ensures consistent product quality.
Common Industries Utilizing Ecoating
Various industries leverage the benefits of ecoating, including:
- Automotive Industry: Provides superior corrosion protection for vehicle parts.
- Appliance Manufacturers: Commonly used for washers, dryers, and other home appliances.
- Electronics: Essential for creating durable and functional circuit boards and components.
- Furniture: Enhances outdoor and metal furniture by offering resistance to weather-related wear and tear.
Choosing the Right E-Coating Service
What to Look for in a Provider
Selecting an e-coating service provider requires careful consideration. Key factors to evaluate include:
- Experience and Reputation: Choose a provider with a track record of successful e-coating projects within your specific industry.
- Quality Control Processes: Ensure they have stringent quality control measures in place to provide consistency in application.
- Technology and Equipment: Modern, well-maintained equipment often translates to better results.
- Flexibility and Service: A good provider should be responsive to your needs, offering customized solutions where necessary.
Cost Factors in Ecoating Services
Understanding the cost structure of e-coating services can help you budget effectively. Factors affecting pricing include:
- Material Type: Different substrates may require varying levels of preparation and treatment.
- Volume and Size of Parts: Larger projects often benefit from economies of scale, while smaller runs might cost more per piece.
- Customization Requirements: Additional finishes or unique colors will increase costs.
- Turnaround Time: Rush orders may incur premium charges.
Evaluating Quality and Results
To ensure that the e-coating service meets your expectations, consider implementing the following evaluation methods:
- Visual Inspection: Check for uniformity in color and finish, as well as the absence of drips or imperfections.
- Thickness Measurement: Utilizing a coating thickness gauge helps verify that the application meets your specifications.
- Adhesion Testing: Conduct a tape test to evaluate how well the coating adheres to the substrate.
- Corrosion Testing: Assess the performance of the coating under challenging environmental conditions to ensure durability.
Ecoating vs Traditional Coating Methods
Comparative Advantages of Ecoating
When juxtaposed with traditional coating methods, such as spray painting, e-coating presents several advantages:
- Uniform Coverage: E-coating guarantees a uniform finish, even on complex surfaces and shapes.
- Reduced Waste: The process is designed to recycle excess paint, minimizing environmental impact.
- Lower VOC Emissions: E-coating typically involves fewer volatile organic compounds than traditional methods.
- Superior Protection: The chemical bonding during the e-coating process results in tougher, more durable layers.
Environmental Impact and Sustainability
Ecoating is increasingly favored for its reduced environmental impact and sustainable qualities:
- Resource Efficiency: The closed-loop system often used in e-coating reduces waste, leveraging almost all paint for application.
- Energy Savings: Modern e-coating facilities employ energy-efficient systems that lower overall energy requirements.
- Health Safety: Low levels of hazardous materials and compliance with regulations promote a safer working environment.
When to Choose Ecoating Over Other Methods
While e-coating is ideal for many applications, it excels especially in:
- Heavy-Duty Applications: Perfect for components that must resist extreme environments.
- Intricate Components: If products feature complex shapes or tight tolerances, e-coating ensures thorough coverage.
- High-Volume Production: E-coating can be more cost-effective than traditional methods due to its high throughput capabilities.
Future Trends in E-Coating
Innovations in Electrocoating Technology
The landscape of e-coating is continually evolving, driven by technological advancements. Emerging trends include:
- Smart Coatings: Incorporating sensors within coatings to monitor wear and environmental conditions in real time.
- Nanotechnology: Enhancing coatings with nanoparticles can significantly improve their properties, such as resistance to wear and corrosion.
- Automated Processes: Automation continues to bring efficiency gains and consistency in e-coating setups.
Market Demand for Ecoating Services
As industries increasingly prioritize longevity and eco-friendliness, the demand for e-coating services is likely to grow:
- Green Initiatives: Many manufacturers are looking for sustainable solutions that comply with regulations and consumer expectations.
- Cost Savings: Companies are recognizing the long-term benefits of investing in e-coating technology for reduced maintenance costs.
- Global Shift Towards Durability: As products become more sophisticated, the need for reliable and robust coatings grows across sectors.
The Role of Ecoating in Industrial Applications
E-coating is becoming a standard in various industrial applications due to its remarkable efficiency and protective properties:
- Automotive Parts: Ensuring corrosion protection on vehicles and equipment used in harsh environments.
- Construction Equipment: Providing solid protection against the elements for heavy machinery.
- Consumer Goods: Offering an aesthetic finish along with the required durability for everyday products.