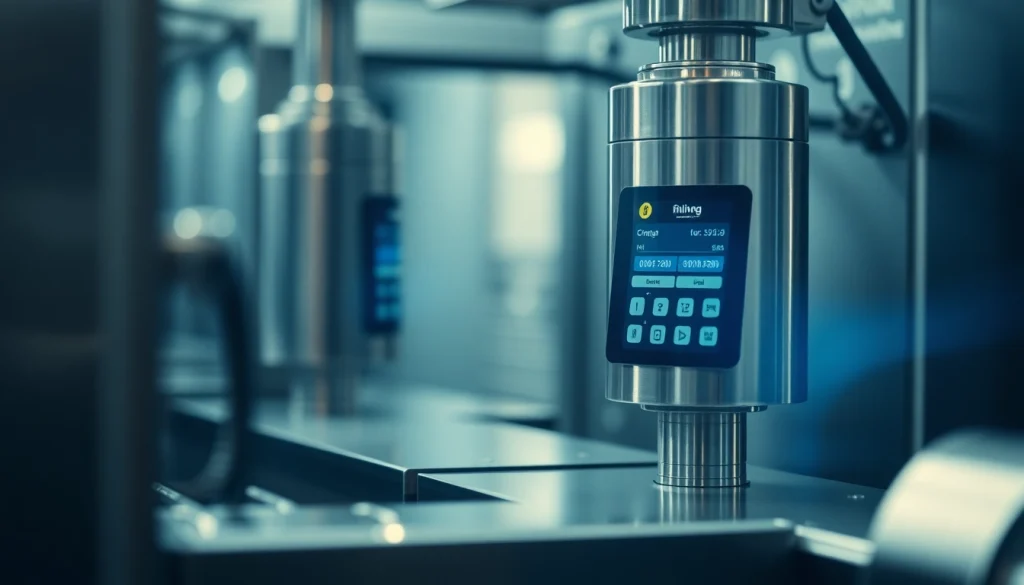
Understanding Filling Machines
What is a Filling Machine?
A filling machine is a crucial apparatus found in various industries, tasked with delivering a predetermined volume of liquid, powder, or granules into containers. By automating the filling process, these machines enhance production efficiency, ensure product consistency, and minimize wastage. Filling machines are highly customizable, catering to various products such as beverages, cosmetics, pharmaceuticals, and even food items. An investment in a Filling Machine can substantially improve both productivity and quality in manufacturing operations.
Types of Filling Machines
Filling machines come in various configurations, each tailored to accommodate different production needs and products. Below are the major types:
- Manual Filling Machines: Operated entirely by hand, these machines are ideal for small-scale operations or specialty products. They often require a higher labor input but are cost-effective for limited production runs.
- Semi-Automatic Filling Machines: Combining manual operation with semi-automatic features, these machines streamline the filling process, requiring operators to perform specific tasks while the machine handles the bulk of the operation.
- Fully Automatic Filling Machines: These represent the pinnacle of efficiency, where the entire process is controlled by a computer system. They can fill large quantities with minimal operator intervention, making them suitable for large-scale manufacturing.
- Piston Filling Machines: Mostly used in liquid filling, these machines utilize a piston mechanism to ensure accurate and consistent fills, making them ideal for thick or viscous products.
- Vacuum Filling Machines: Employed mainly for liquid products, vacuum filling operates through suction, allowing for controlled filling while minimizing air bubbles, thus ensuring product integrity.
Key Components and Technology
Filling machines depend on several key components that contribute to their functionality and efficiency:
- Filling Nozzle: The nozzle controls the flow of the substance being filled, often designed to minimize spills and drips.
- Control System: Advanced filling machines come equipped with programmable logic controllers (PLCs) that monitor operations and ensure precision during filling cycles.
- Conveyor Belt: A conveyor belt system is essential for transporting containers seamlessly through the filling process.
- Sensors: Modern filling machines incorporate sensors for detecting the presence of containers, measuring fills, and enhancing accuracy in operation.
- Pump Mechanisms: Depending on the filling machine type, various pumps (gear, diaphragm, peristaltic) provide the necessary force to move the product into containers.
Applications of Filling Machines
Industries Using Filling Machines
Filling machines are utilized across numerous industries where precise filling is essential. Some primary sectors include:
- Food and Beverage: Automating the filling of liquids, sauces, and powdered foods enhances hygiene and consistency in this sector.
- Pharmaceutical: In the pharmaceutical industry, filling machines fill vials and syringes with precision, adhering to strict regulatory standards.
- Cosmetics: For the beauty industry, filling machines help dispense creams, lotions, and fragrances effectively, ensuring consistent product quality.
- Chemicals: Chemical manufacturers rely on robust filling machines to handle hazardous liquids and powders while maintaining safety protocols.
Choosing the Right Filling Machine for Your Needs
Choosing the appropriate filling machine involves several considerations:
- Product Type: You need to assess whether your product is a liquid or dry substance, viscous or thin, as this will dictate the machine type.
- Production Volume: Evaluate your production scale. High volumes favor fully automatic systems, while low volumes might make manual systems more cost-effective.
- Budget Constraints: Factor in both initial purchase costs and long-term operating expenses, including maintenance and any potential upgrades.
- Space Availability: Ensure that the layout of your facility can accommodate the chosen machine without hindering workflow.
Case Studies: Successful Implementations
To illustrate the impact of filling machines in real-world scenarios, consider a scenario in the beverage industry:
A mid-size juice manufacturer faced issues with inconsistent fills and high waste levels, leading to customer complaints. They replaced their manual filling system with a fully automatic filling machine that utilized volumetric filling technology. This change resulted in:
- A 40% reduction in product waste.
- Production rates increased by 70%, allowing for quicker product turnover.
- Product consistency improved, ultimately enhancing customer satisfaction and loyalty.
Benefits of Investing in Filling Machines
Increase Efficiency and Reduce Waste
One of the most significant benefits of filling machines is their ability to increase operational efficiency. By automating repetitive tasks, they significantly reduce the time taken to fill containers compared to manual methods. Furthermore, precise filling minimizes wastage, a critical factor for companies seeking to improve profitability.
Enhancing Product Consistency
Whether filling bottles with liquids or jars with powdered substances, filling machines maintain product consistency. This ensures that each container meets the same quality standards, essential in nurturing brand reputation. Automated machines are programmed to deliver precise volumes, eliminating the variability often inherent in manual filling processes.
Cost Savings Over Time
Although purchasing a filling machine may require upfront investment, the long-term savings can be substantial. Reduced labor requirements, lower product waste, and increased production efficiency contribute to a healthier bottom line. Additionally, many filling machines are designed for durability and longevity, further enhancing their return on investment.
Maintenance and Troubleshooting
Routine Maintenance Steps for Optimal Performance
To keep filling machines running smoothly, regular maintenance is critical. Here are a few maintenance tips:
- Conduct scheduled cleaning to remove any residue buildup.
- Inspect the filling nozzles and pumps regularly for signs of wear.
- Lubricate moving parts to avoid mechanical failures.
- Regularly calibrate the control systems to ensure ongoing precision during operation.
Common Issues and Solutions
Operators may encounter various challenges when using filling machines. Here are a few common issues along with their solutions:
- Inconsistent Fills: This could result from a faulty nozzle or improper calibration. Regularly checking and calibrating the machine should rectify this issue.
- Leaks: If there are leaks, inspect the filling nozzles and seals for wear and replace any compromised parts immediately.
- Slow Filling Speed: Performance might drop due to improper settings. Reviewing the machine settings and confirming they match the product specifications is advisable.
When to Seek Professional Help
If routine maintenance does not resolve issues or if problems recur frequently, it may be time to seek professional assistance. Engaging technicians familiar with your specific filling equipment can help diagnose and rectify persistent issues effectively. Keeping a service contract on hand with a reputable provider can prevent prolonged downtimes and unexpected costs.
Future of Filling Technology
Innovative Features in Modern Filling Machines
The filling technology landscape is continually evolving, driven by innovations that enhance efficiency and usability.
Modern filling machines are increasingly integrating features such as:
- Smart Technology: IoT integration allows operators to monitor machine performance remotely, adjust settings on-the-fly, and receive alerts about potential issues.
- Eco-friendly Solutions: Filling machines are designed with sustainability in mind, with options for less energy consumption and reduced plastic waste.
- Flexible Filling: Multi-purpose machines can switch between product types quickly, accommodating diverse production needs without significant downtime.
Adapting to Industry Trends
As consumer preferences shift towards sustainability and personalization, filling machines will need to adapt to meet these demands. Companies are responding by investing in technologies that support smaller batch sizes and enhanced customization features.
Automated vs. Manual Filling Machines: The Future Landscape
While manual filling machines will likely always have a place in small-scale operations, the trend is steadily shifting toward automation. As technology progresses and costs decrease, even smaller companies may find the initial investment for fully automated systems justifiable based on efficiency gains and long-term savings. Understanding this trend is crucial for businesses looking to future-proof their operations and remain competitive in an evolving marketplace.