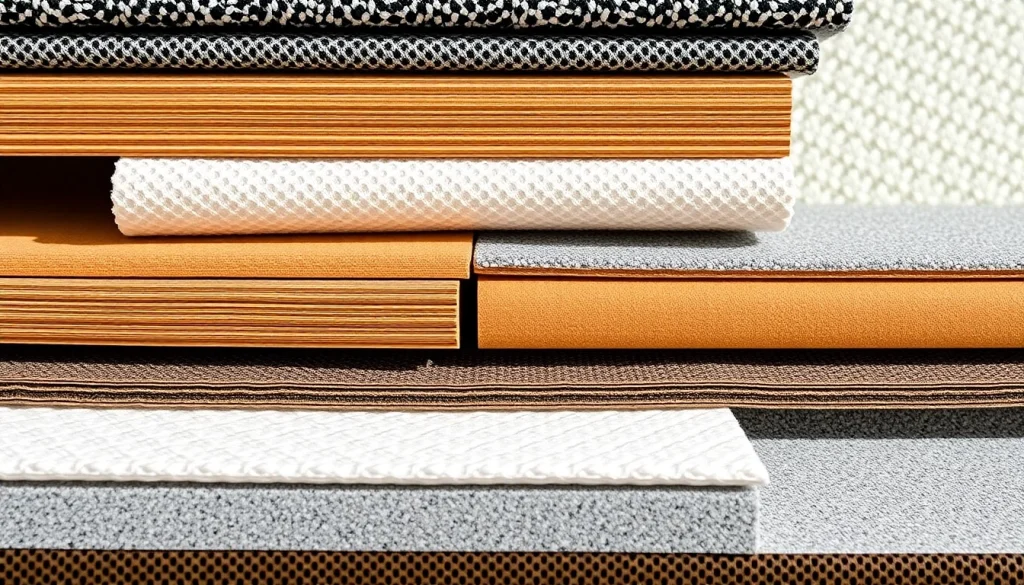
Understanding Thermal Management Materials
In the fast-paced world of technology, the need for effective thermal management is essential for the reliable functioning of electronic devices. As devices become smaller and more powerful, managing the heat they generate is critical for performance and longevity. Thermal management materials play a crucial role in this area by providing solutions to dissipate heat efficiently and ensure optimal performance of electronic components.
What are Thermal Management Materials?
Thermal management materials are specialized substances designed to regulate temperature in various applications, particularly in electronics. These materials facilitate heat transfer, aiming to prevent overheating, enhance cooling efficiency, and ultimately prolong the life of electronic components. The effectiveness of these materials is measured by their thermal conductivity, which dictates how well they can conduct heat away from critical areas of a device.
Common types of thermal management materials include thermal interface materials (TIMs), thermal pads, gap fillers, thermal adhesives, and thermal tapes. Each of these materials has specific properties and is designed for different applications, ranging from consumer electronics to industrial machinery.
The Importance of Thermal Management in Electronics
The increasing power density of modern electronics leads to significant heat production. Effective thermal management is vital for several reasons:
- Enhanced Reliability: Overheating can lead to component failure; thus, efficient thermal management ensures the longevity of devices.
- Improved Performance: High temperatures can degrade performance; maintaining optimal operating temperatures enhances efficiency.
- Safety: Excessive heat can pose safety hazards, making thermal management essential for safe operation in devices.
As technology continues to advance, incorporating superior thermal management materials becomes increasingly crucial for maintaining device integrity.
Types of Thermal Management Materials
Understanding the diverse types of thermal management materials is essential for selecting the appropriate one for particular applications. Here are several key types:
Thermal Interface Materials (TIMs)
TIMs are commonly used in electronic assemblies to improve the thermal connection between components like microprocessors and heat sinks. They fill microscopic air gaps that would otherwise impede heat transfer. Examples include thermal pastes, pads, and gels.
Thermal Pads
These are soft, flexible materials that conform to surfaces to enhance heat transfer. They are often used in applications where rigid materials cannot fit snugly or where high adaptability is required.
Gap Fillers
Gap fillers are used to bridge the thermal gap between heat-generating components and heat sinks. They maintain optimal thermal conductivity while compensating for misalignments in component surfaces.
Thermal Adhesives
These adhesives not only bond components but also provide thermal conductivity. They are particularly useful in applications requiring both adhesion and effective heat transfer.
Thermal Tapes
Designed for easy application, thermal tapes are often used to attach heat sinks to components or secure thermal pads. Their adhesive properties and thermal conductivity make them versatile solutions.
Applications of Thermal Management Materials
The applications of thermal management materials are vast and varied, encompassing consumer electronics, industrial machinery, and innovative technological developments.
Use Cases in Consumer Electronics
In consumer electronics such as smartphones, tablets, and laptops, thermal management materials are essential. These devices host advanced processors that generate significant heat; hence, employing TIMs ensures effective heat dissipation, preventing performance throttling.
For instance, high-performance gaming laptops often use thermal pads and gap fillers to maintain optimal temperatures during intense gaming sessions, thus enhancing user experience and device reliability.
Industrial Applications and Solutions
Beyond consumer electronics, thermal management materials find extensive use in industrial applications, including manufacturing equipment, telecommunications, and automotive industries. High-power electronic components in these sectors often require advanced thermal solutions like phase change materials and custom thermal adhesives to ensure consistent performance amid demanding conditions.
In the automotive sector, for instance, robust thermal management materials are critical for electric vehicles (EVs) to manage battery heat efficiently, ensuring safety and prolonging battery life.
Innovations in Thermal Management
Research and development in thermal management materials are continuously evolving. Innovations include the development of advanced materials that possess higher thermal conductivity and reduced thermal resistance, which enhances the overall efficiency of electronic systems.
Nanotechnology, for example, is being explored to create materials with enhanced heat transfer properties, which could revolutionize thermal management in electronics and other industries.
Key Considerations When Choosing Thermal Management Materials
Selecting the appropriate thermal management material involves understanding various factors that can influence its performance.
Factors Affecting Thermal Conductivity
Several key factors affect the thermal conductivity of materials, including:
- Material Composition: Different materials exhibit varying levels of thermal conductivity. For example, metals like copper and aluminum have high thermal conductivity compared to plastics.
- Density: Generally, denser materials tend to conduct heat more effectively.
- Thickness: The thickness of the material can also impact performance; thinner materials might provide more efficient heat transfer in certain applications.
How to Select the Right Material for Your Needs
When selecting a thermal management material, it is vital to consider the specific requirements of your application, including:
- Operating Temperature Range: Choose materials that can withstand the maximum and minimum temperatures expected in your application without degrading.
- Mechanical Properties: Evaluate the flexibility, hardness, and compressibility of materials in relation to the application.
- Environmental Resistance: Consider materials that can resist moisture, chemicals, and other environmental factors that might affect performance.
Cost vs. Performance: Making the Right Choice
Often, there is a balancing act between cost and performance when choosing thermal management materials. While premium materials may offer superior thermal conductivity or longevity, budget constraints may necessitate a more economical choice.
Thus, it’s essential to conduct a thorough cost-benefit analysis, assessing the total cost of ownership versus the long-term benefits of investing in higher-quality materials. This decision-making process should also take into account the potential costs associated with equipment downtime or failures due to inadequate thermal management.
Best Practices for Implementing Thermal Management Solutions
Effective implementation of thermal management solutions requires careful planning and execution. Below are some best practices to follow.
Installation Tips for Optimal Performance
Proper installation is crucial for maximizing the efficacy of thermal management materials. Here are several tips:
- Surface Preparation: Ensure that all surfaces are clean and free from contaminants. Any dirt, grease, or residue can impair thermal conduction.
- Correct Application: Follow manufacturer instructions for applying thermal pastes, adhesives, or pads, including recommended thickness and curing times.
- Use of Spacers: In some cases, using spacers can help maintain pressure between components, enhancing thermal contact.
Maintaining Efficiency Over Time
Regular maintenance is essential in ensuring that thermal management solutions continue to perform effectively. This can include:
- Periodic Inspections: Regularly check for signs of wear, degradation, or excessive thermal buildup, especially in high-demand applications.
- Material Replacement: Consider replacing thermal pads or pastes after a specified period to maintain efficiency.
Crisis Management in Thermal Design
In the event of thermal failure, have a crisis management plan in place. This may include:
- Emergency Cooling Systems: Implement backup systems that can temporarily relieve overheating issues.
- Data Monitoring: Use temperature monitoring equipment to detect overheating before it leads to failure.
The Future of Thermal Management Materials
As technology advances, so too does the field of thermal management materials. Emerging trends and innovations present exciting opportunities for improved solutions.
Emerging Trends in Material Science
Innovations in material science are paving the way for new types of thermal management solutions. Advances in phase change materials (PCMs) can provide passive cooling, while smart materials that change properties in response to thermal conditions are also emerging.
These developments promise enhanced energy efficiency and performance, which will be crucial for the growing market of electric vehicles and renewable energy solutions.
Environmental Impact and Sustainability
Sustainability is increasingly becoming a critical factor in the choice of materials. The demand for eco-friendly thermal management materials is growing, reflecting broader environmental concerns. Manufacturers are researching biodegradable materials that can effectively manage heat without the environmental impact of traditional options.
Future Innovations to Watch For
The future holds significant potential for further innovations in thermal management materials, including:
- Hybrid Materials: Combining different material properties to optimize performance across thermal management applications.
- Nanomaterials: Utilizing nanoscale structures to significantly enhance thermal conductivity, reducing energy consumption.
Staying abreast of these trends will be crucial for engineers and designers as they seek to improve thermal management in increasingly sophisticated electronic devices.