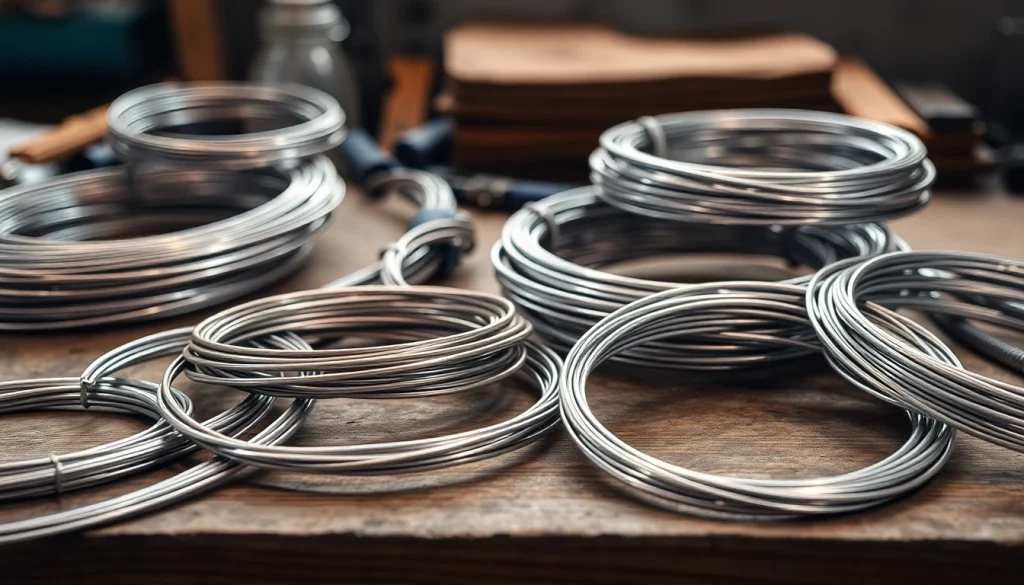
Introduction to Stainless Steel Wire
Stainless steel wire is an essential material used across numerous industries, from construction to manufacturing, due to its impressive properties. Often synonymous with durability and resistance to corrosion, stainless steel wire comes in various grades and formulations, all designed to meet specific environmental and operational demands. As industries evolve and require more efficient materials, understanding stainless steel wire’s characteristics, applications, and maintenance becomes increasingly crucial for both seasoned professionals and newcomers alike.
What is Stainless Steel Wire?
Stainless steel wire is a wire made from an alloy of iron, chromium, and sometimes other elements like nickel or molybdenum. This combination confers on the wire its characteristic resistance to corrosion and staining, making it a popular choice for various applications. The process for producing stainless steel wire involves melting and alloying the raw materials, followed by drawing the resulting ingots into wires of varying gauges and sizes. This process ensures that the final product retains the desired properties while achieving the necessary dimensional accuracy.
Key Characteristics of Stainless Steel Wire
The distinct characteristics of stainless steel wire can be summarized as follows:
- Corrosion Resistance: Stainless steel wire exhibits remarkable resistance against rust and corrosion, particularly in harsh environments.
- Tensile Strength: It can handle heavy loads and stress, making it suitable for construction and industrial applications.
- Durability: The wire can withstand wear and tear, prolonging its life in demanding environments.
- Industrially Versatile: It is adaptable for use in various applications, including but not limited to electrical, construction, and jewelry.
Applications Across Industries
Stainless steel wire finds applications in a plethora of industries:
- Construction: Used for reinforcement in concrete, binding, and other structural applications.
- Manufacturing: Ideal for creating various products, from automotive components to appliances.
- Medical: Preferred in surgical instruments and devices due to its sterility and strength.
- Marine: Utilized in boat rigging and fittings owing to its corrosion resistance in saltwater.
- Jewelry Making: Commonly for crafting highly durable and hypoallergenic pieces.
Types of Stainless Steel Wire
Common Grades of Stainless Steel Wire
Stainless steel wire is available in different grades, each offering unique properties suited to specific applications. The most common grades include:
- 304 Stainless Steel: The most popular type, known for its excellent corrosion resistance and formability, ideal for many applications, including kitchen utensils and food processing equipment.
- 316 Stainless Steel: Contains molybdenum, providing superior resistance to pitting and crevice corrosion in more aggressive environments, such as marine applications.
- 430 Stainless Steel: A ferritic stainless steel that is less corrosion-resistant than austenitic grades but provides good oxidation resistance and is suitable for decorative applications.
Different Forms of Stainless Steel Wire
Stainless steel wire can be categorized into several forms:
- Solid Wire: Useful for creating stronger connections; commonly used in construction and industrial applications.
- Stranded Wire: Composed of several strands twisted together, offering flexibility and reduced stress on each wire, making it ideal for applications like electrical cabling.
- Coated Wire: Often coated with PVC or nylon for additional protection and insulation, suitable for outdoor and marine applications.
Comparison of Stainless Steel Wire Types
The choice of stainless steel wire type depends on the specific requirements of the application:
- Strength vs. Flexibility: Solid wires are strong but less flexible compared to stranded wires, which can bend and flex under tension.
- Cost vs. Performance: While high-grade stainless steel wires (like 316) offer superior performance, they come at a higher cost than lower-grade options.
- Corrosion Resistance: Applications in harsh environments typically require higher corrosion-resistant grades, even if they increase overall project costs.
Choosing the Right Stainless Steel Wire
Factors to Consider When Selecting Wire
Selecting the right stainless steel wire requires careful consideration of several factors, including:
- Application Requirements: Understand the specifics of the application, such as load requirements, environmental conditions, and corrosion risks.
- Gauge and Diameter: The thickness of the wire influences its strength and application suitability; heavier gauges provide more strength but less flexibility.
- Environmental Factors: Acknowledge the surrounding conditions, such as exposure to moisture, chemicals, or high temperatures, that can impact the wire’s performance.
Typical Uses for Various Wire Types
Different types of stainless steel wire have typical uses, including:
- 304 Wire: Most commonly used in commercial kitchens and food processing plants.
- 316 Wire: Preferred in marine and saltwater applications, like rigging and mooring lines.
- Low-Alloy Wires: Used in lighter applications, including hobbyist and craft projects.
Common Mistakes in Wire Selection
Here are some common pitfalls to avoid when selecting stainless steel wire:
- Ignoring Corrosion Risks: Failing to consider the environmental corrosion challenges can lead to wire failure.
- Overlooking Mechanical Properties: Using a wire that is either too thin or too thick for the application can compromise performance.
- Disregarding Manufacturer Specifications: Each wire type comes with specific guidelines; disregarding these can lead to safety and performance issues.
Benefits of Using Stainless Steel Wire
Corrosion Resistance Explained
One of the foremost reasons for choosing stainless steel wire is its exceptional resistance to corrosion. This resistance is a result of the chromium content in the alloy, which forms a passive layer over the surface of the steel, protecting it from environmental factors. In applications such as construction and outdoor installations, where moisture and chemicals may be prevalent, this property ensures longevity and reduced maintenance costs.
Strength and Durability
Stainless steel wire is known for its high tensile strength and durability, making it ideal for heavy-duty applications. Whether it’s in construction, automotive, or marine industries, the strength of stainless steel wire supports structural integrity and safety. Its ability to withstand extreme temperatures and physical wear ensures that structures stay resilient over time.
Versatility in Applications
The versatility of stainless steel wire allows it to be used in a wide range of applications. From jewelry making to industrial rigging, the options are limitless. Its resistance to rust and ability to maintain a clean appearance make it suitable in aesthetic applications like railings and art installations, while its strength is vital in rigging and structural applications.
Maintenance and Care for Stainless Steel Wire
Cleaning and Polishing Techniques
To preserve the quality of stainless steel wire, regular cleaning is essential. Generally, a mild detergent mixed with warm water, applied with a non-abrasive sponge, is sufficient for cleaning. In cases of tougher stains, solutions like baking soda paste can be effective. Polishing with a microfiber cloth can restore shine and luster, enhancing its appearance and preventing tarnishing.
Storing Stainless Steel Wire Safely
Safe storage of stainless steel wire is crucial in preventing physical damage and contamination. It is advised to store wire in a dry, cool area, away from excessive moisture and direct sunlight. If possible, placing it in a sealed container can protect against dust and other environmental factors.
Recognizing Damage and Quality Checks
Regular inspections of stainless steel wire should include a check for signs of damage, such as kinks, bends, or corrosion spots. If any of these issues are present, it’s crucial to replace the damaged wire to maintain safety and performance. Additionally, purchasing from reputable manufacturers ensures the quality of the wire adheres to industry standards.