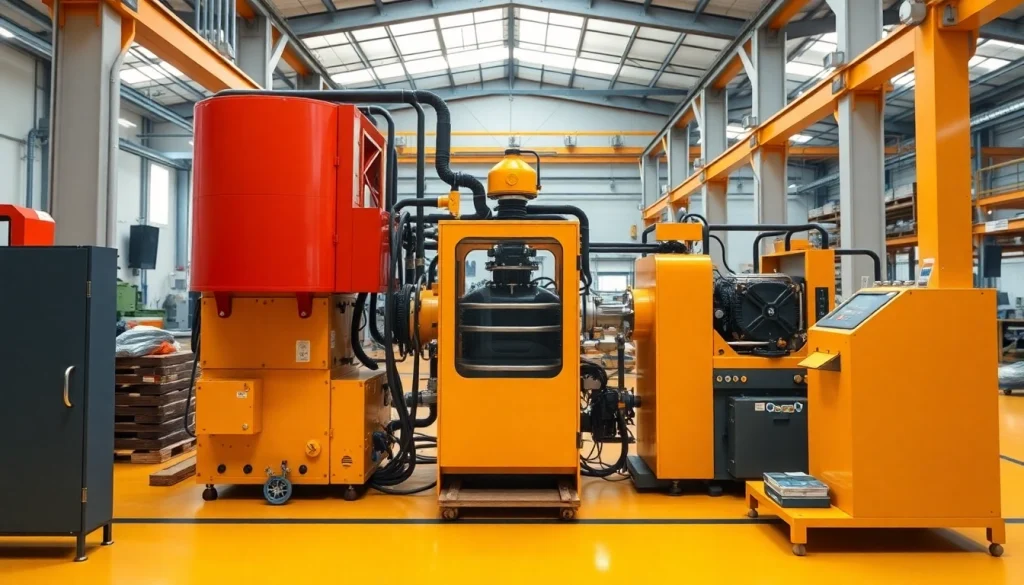
Introduction to Filling Machines
Filling machines play a crucial role in various industries by automating the process of depositing precise amounts of liquid, powders, or granules into containers. With the advancement of technology, these machines have evolved to enhance efficiency and accuracy in production lines. This article aims to provide a comprehensive guide to filling machines, discussing their types, benefits, maintenance, and selection factors. For more detailed information about a specific Filling Machine, it is recommended to explore dedicated resources available online.
What is a Filling Machine?
A filling machine is a type of industrial equipment used to dispense a specific amount of liquid, powder, or other substances into containers such as bottles, jars, or pouches. These machines are essential for ensuring consistent quality and quantity in the packaging process, especially in industries like food and beverage, pharmaceuticals, and cosmetics. Filling machines can operate based on several principles including weight, volume, and time, enabling them to fit various production needs.
The Historical Development of Filling Machines
The concept of filling machines dates back to the late 19th century when the industrial revolution paved the way for mechanized processes in manufacturing. Early models were simple and often required manual operation. Over the decades, innovations led to the development of semi-automatic and fully automatic machines that increased production rates and reduced labor costs. Today, modern filling machines utilize advanced technologies such as digital controls and precision pumps, allowing for greater accuracy and faster operation.
Main Applications in Industry
Filling machines are integrated into various industries due to their versatility. Major applications include:
- Food and Beverage: Filling machines are used to package drinks, sauces, and other liquid foods, ensuring they meet food safety standards.
- Pharmaceutical: In this sector, precision is vital. Filling machines are used to package syrups, capsules, and solutions in regulated environments.
- Cosmetics: Products such as lotions and creams require filling machines to maintain consistency across batches.
- Chemical: Filling machines handle various chemicals, including hazardous substances, demanding strict safety protocols.
Types of Filling Machines
Manual Filling Machines
Manual filling machines require human intervention for operation. They are typically used for smaller production runs or in operations where the filling volume is small and variability is acceptable. Manual machines may include gravity fillers or piston fillers, where an operator controls the filling process. While economic, they can be slower and less consistent than automated solutions.
Semi-Automatic Filling Machines
Semi-automatic filling machines strike a balance between manual and fully automatic systems. They require some operator intervention, such as placing containers and starting the filling process, but they automate the actual dispensing of the product. These machines are suitable for medium-sized production lines and offer improved consistency and speed compared to manual machines.
Fully Automatic Filling Machines
Fully automatic filling machines operate independently and require minimal human input. They are highly sophisticated, equipped with sensors and controls that enable them to monitor and adjust the filling process in real time. Ideal for high-volume production environments, these machines can fill containers at speeds exceeding hundreds per minute. Technologies include vacuum fillers, pump fillers, and level sensors to ensure accuracy.
Benefits of Using Filling Machines
Time and Cost Efficiency
One of the most significant advantages of filling machines is the time and cost savings they provide. Automated machines can fill containers faster than manual labor, significantly speeding up production lines and reducing operational costs associated with labor.
Increased Accuracy and Consistency
Filling machines minimize human error, ensuring a consistent fill every time. This accuracy is crucial in industries like pharmaceuticals and food production, where precise measurements affect compliance and consumer safety. Automated systems can be calibrated to specific measurements, allowing businesses to maintain standards across batches.
Reduced Waste and Errors
By using advanced technologies, filling machines help reduce product waste and packaging errors. They can implement features such as nozzles that prevent drips or automatic shut-offs that stop filling once the container is full. This reduction in waste is not only economical but also environmentally friendly.
Selecting the Right Filling Machine
Consider Production Needs
When choosing a filling machine, it is essential to consider production volume and the types of products to be filled. High-volume production lines will benefit from fully automatic machines, while smaller operations may find manual or semi-automatic machines more practical.
Assess Technical Specifications
Evaluating the technical specifications of filling machines, such as fill rates, container sizes, and the types of products that can be processed (liquids, powders, etc.), is vital to ensure compatibility with production requirements. Additionally, consider factors like ease of operation, cleaning, and maintenance.
Budget and ROI
Lastly, it’s crucial to evaluate the budget for acquiring a filling machine, as prices can vary widely based on technology and specifications. Consider the return on investment (ROI) by analyzing savings in labor, increased production efficiency, and reduced waste. This financial analysis will help determine the most cost-effective option in the long term.
Maintenance and Care of Filling Machines
Importance of Routine Maintenance
Regular maintenance is critical to ensure reliable operation and prolong the lifespan of filling machines. Scheduled checks for wear and tear, cleaning components, and ensuring lubrication can prevent significant issues down the line. A maintenance plan should be established based on the manufacturer’s recommendations.
Maintenance Tips and Tricks
Here are some practical tips for maintaining filling machines:
- Regularly inspect seals and gaskets for wear and replace them as needed.
- Clean the filling nozzles after each production run to prevent clogs.
- Keep the machine’s exterior clean to avoid contaminating the production area.
- Document all maintenance activities to track machine performance over time.
Why Consult Professionals?
While routine maintenance can be performed by operational staff, it is advisable to consult professional technicians for major repairs or when troubleshooting issues that could impact production. Professionals bring extensive knowledge and experience, ensuring that repairs and adjustments are correctly handled without risking further damage to the equipment.