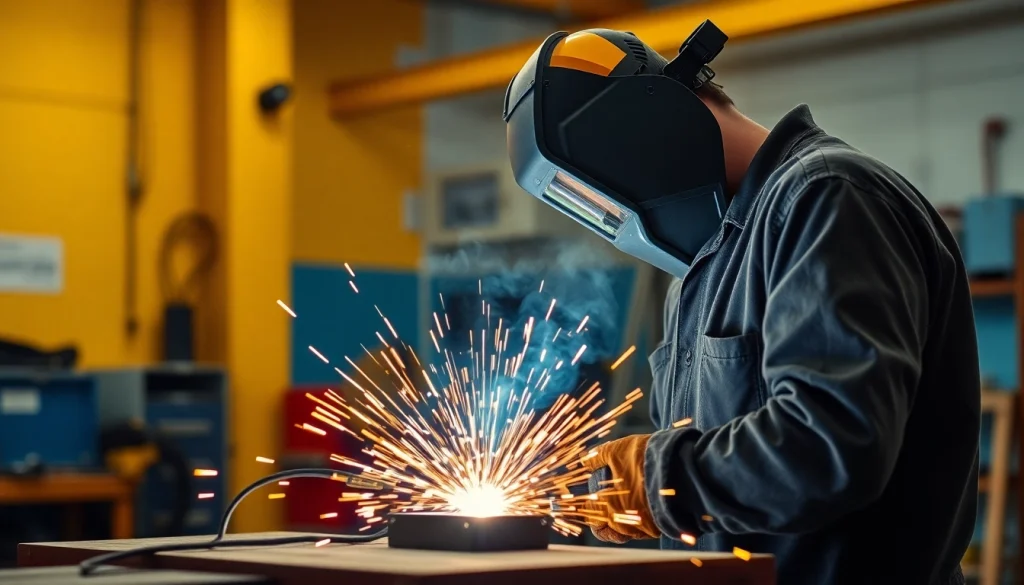
Understanding AC DC TIG Welders
What is an AC DC TIG Welder?
An AC DC TIG welder is a sophisticated welding machine that uses tungsten inert gas (TIG) welding technology. This type of welder is capable of operating on both alternating current (AC) and direct current (DC), providing unmatched flexibility in welding applications. AC is generally used for welding non-ferrous metals such as aluminum, whereas DC is preferred for ferrous metals like steel and stainless steel. The versatility of an ac dc tig welder makes it ideal for a wide range of industries, from automotive and aerospace to construction and fabrication.
How AC DC TIG Welding Works
At its core, TIG welding employs a non-consumable tungsten electrode to produce a weld. The welder generates an electric arc between the tungsten electrode and the workpiece, melting the base metal and allowing for the addition of filler material if necessary. When using AC, the welder generates alternating cycles of electricity, which helps clean the oxide layer off aluminum and promotes better fusion. Conversely, DC provides a constant flow of electricity, allowing for a more stable arc and longer electrode life.
Benefits of Using an AC DC TIG Welder
- Versatility: The ability to work with a variety of metals, including aluminum, stainless steel, and magnesium.
- Precision: TIG welding is known for its clean and precise welds, making it ideal for critical applications.
- Control: Welders have better control over the weld pool, allowing for fine adjustments to be made.
- Minimized Heat Affected Zone: The focused heat of the welding arc leads to less distortion and a smaller heat-affected zone.
- Portability: Many modern AC DC TIG welders are compact and lightweight, allowing for easy transport.
Choosing the Right AC DC TIG Welder
Key Features to Look For
When selecting an AC DC TIG welder, it’s crucial to consider several features that will impact your welding experience:
- Amperage Range: Ensure the welder has a suitable amperage range for your projects; higher amps are needed for thicker materials.
- Pulse Control: Pulse features allow for better heat control, leading to improved aesthetics in the weld.
- Portability: If you need to transport your welder, look for lightweight and compact models.
- Digitization: Digital displays can make fine-tuning settings easier, especially for beginners.
- Duty Cycle: Higher duty cycles mean more continuous welding time without overheating the unit.
Top Brands and Models
Several brands have established themselves as leaders in the AC DC TIG welding market. Notable mentions include:
- Miller Electric: Known for their robust and reliable welders, such as the Miller Dynasty and Diversion series.
- Lincoln Electric: Offers models like the Lincoln Square Wave TIG 200, which is praised for its ease of use.
- Everlast: A popular choice for hobbyists and professionals alike, with models like the PowerTIG series.
- PrimeWeld: Known for value-for-money models like the TIG225X, which provide great features at an affordable price.
- Weldpro: Offers quality welders with advanced features, such as their Digital TIG 200GD model.
Price Ranges and Budgeting
Pricing for AC DC TIG welders can vary significantly, typically ranging from $500 to over $5,000 depending on the brand, features, and capabilities. For hobbyists and light-use applications, budget models may suffice, typically costing around $500 to $1,500. For professional-grade welders with advanced features, expect to pay $2,000 and upwards. It’s essential to assess your needs, including materials and frequency of use, to determine the right budget for your welder.
Applications of AC DC TIG Welding
Industries That Utilize AC DC TIG Welders
AC DC TIG welding is widely used across multiple industries due to its precision and versatility:
- Aerospace: Used for critical joints and lightweight components.
- Automotive: Common in fabricating exhaust systems, chassis parts, and more.
- Manufacturing: Ideal for assembling complex machinery where precision is key.
- Construction: Welding structural components and fixtures in buildings.
- Pipe and Tank Fabrication: Ensures strong, leak-proof joints in pressure vessels and piping systems.
Common Projects and Materials
Many projects can benefit from the use of AC DC TIG welders:
- Aluminum fabrication: Ideal for welding thin aluminum sections as well as heavier gauges.
- Stainless steel fabrication: Allows for strong, aesthetically pleasing welds on stainless steel.
- Repair work: Excellent for repairing various metals without the risk of warping.
- Art and sculpture: Artists appreciate the control and finish achieved with TIG welding.
When to Use AC vs. DC?
Understanding when to use AC or DC is crucial for optimal results:
- AC: Best for aluminum and magnesium; effective for cleaning the oxide layer, ensuring better weld quality.
- DC: Preferred for welding steel, stainless steel, and copper; provides a stable arc and better penetration.
Choosing between AC and DC also depends on the thickness of the material, desired penetration, and electrode wear considerations.
Tips for Operating AC DC TIG Welders
Setting Up Your Welder Efficiently
Efficient set-up is critical for achieving high-quality welds. Here are some tips:
- Ensure that all connections are secure and that there are no leaks in the gas line.
- Choose the appropriate tungsten electrode based on the metals and thickness you are welding.
- Set the correct amperage based on the material thickness to avoid burn-through or inadequate fusion.
- Adjust your gas flow rate; typically, 15-20 CFH (cubic feet per hour) is suitable for most applications.
- Conduct a test weld on scrap material to ensure settings are dialed in.
Safety Measures and Best Practices
Safety is paramount in welding, and adhering to best practices is key:
- Always wear protective gear, including welding helmets, gloves, and flame-resistant clothing.
- Ensure proper ventilation in the workspace to avoid harmful fumes.
- Maintain a clean working area to reduce risks of fire and accidents.
- Familiarize yourself with emergency procedures and have fire extinguishers accessible.
- Regularly inspect your equipment for wear and tear and address any issues before starting work.
Maintenance for Longevity
Regular maintenance helps prolong the life of your AC DC TIG welder:
- Regularly clean and inspect the torch and cables for any damage or wear.
- Keep the gas nozzle free of spatter and replace it as needed to maintain a clean gas flow.
- Replace the tungsten electrode regularly to ensure clean, stable arcs.
- Check gas levels frequently and replenish as necessary to avoid interruption during welding.
- Store the welder in a dry, clean environment to protect it from dust and moisture.
Advanced Techniques with AC DC TIG Welders
Transitioning from Beginner to Pro
Once you’ve mastered the basics, consider implementing more advanced techniques:
- Practice varying the speed of the travel and the angle of the torch to achieve different weld profiles.
- Experiment with weaving patterns for wider welds on thicker materials.
- Learn to manipulate the pedal to adjust the heat dynamically during a weld.
- Work on timing between moving the torch and feeding filler material for effective results.
Utilizing Pulse Features
Pulse features can enhance your welding capabilities:
- Pulsed TIG welding allows for better control of heat input, especially on thin materials.
- It reduces the risk of distortion while helping achieve a higher-quality aesthetic finish.
- Practice adjusting pulse frequency and duration to adapt to different materials and thicknesses.
Welding Aluminum vs. Steel
Welding aluminum and steel require different approaches due to material properties:
- Aluminum has a higher thermal conductivity, necessitating adjustments in amperage and technique to prevent burn-through.
- Steel typically allows for more straightforward welding, but attention to heat input is still vital to prevent warping.
- Filler materials vary between metals; use aluminum fillers for aluminum and steel fillers for steel.
In conclusion, selecting and operating an AC DC TIG welder involves understanding its capabilities, applications, and best practices for maintenance. By mastering both the fundamentals and advanced techniques, you can enhance your welding skills and achieve outstanding results in various projects.